Pro-FeAl
Pro-FeAl: Prozessentwicklung für wirtschaftliche, effiziente Turbinenkomponenten aus Eisenaluminiden (Fe-Al)
Ziel
Fokus des Teilprojektes von Access ist die Evaluierung der Technologieroute Gießen+Schmieden zur Verarbeitung von FeAl-Legierungen. Es soll ermittelt werden, welche Legierung zur Fertigung spezifikationsgerechter Bauteile geeignet ist und welche Wechselwirkungen zwischen Prozessroute, Bauteileigenschaften und Bauteilauslegung existieren. Dabei bestehen folgende Ziele:
– Fertigungsrelevantes Prozesswissen für die Herstellung vorkonturierter FeAl Schmiederohlinge: Gießgerechte Konstruktion, Schmelzbetrieb, Formenbau und Formstoffauswahl, Gießprozessführung
– Wechselwirkungen zwischen Bauteildesign, Prozessführung, Legierung und Bauteileigenschaften
– Charakterisierung der Bauteile: Korngrößen, Gefüge,…
– Datenbasis für Gieß- und Erstarrungssimulationen
– Wirtschaftlichkeitsbewertung
Kurzbeschreibung
Das Pro-FeAl-Vorhaben von Access befasst sich mit der hybriden Herstellungsroute Gießen+Schmieden zur Fertigung von hochbelasteten Bauteilen mit Einsatztemperaturen bis 700 °C. Für diese Prozessroute wird untersucht, welche Legierungskonzepte geeignet sind, wie die wesentlichen Bauteileigenschaften wie Festigkeit, Ermüdung und Duktilität von der Prozessroute und dem Bauteildesign abhängen und wie sich diese Eigenschaften gezielt durch Einstellung und Abstimmung der Prozesse Gießen+Schmieden für die in Frage kommenden Legierungen beeinflussen lassen.
Die Herstellung von geschmiedeten Bauteilen für Hochtemperaturanwendungen aus vorkonturierten Schmiederohlingen bietet wesentliche Potentiale zur Realisierung von Vorteilen im Vergleich zum Schmieden aus nicht vorkonturiertem Material. Dazu gehören ein reduzierter Materialeinsatz, optimierte Bauteilgefüge und der Wegfall einer Schmiedestufe. Mit der Entwicklung einer für das Schmieden optimierten Geometrie des Gussrohlings kann damit, neben der Reduktion des Materialeinsatzes, auch der sonst notwendige kosten- und zeitaufwendige Prozessschritt der vor dem Fertigschmieden erforderlichen Volumenverteilung entfallen. Als besonders anspruchsvoll erweist sich in diesem Zuge die Entwicklung einer Formtechnologie für den Guss, die die Herstellung von konturierten Rohlingen mit typischen geometrischen Merkmalen, wie z.B. den Deckbändern bei Verdichterschaufeln, erlaubt. Insbesondere Risse im Gussrohling, die aufgrund zu hoher Eigenspannungen während der Erstarrungs- und Abkühlphase entstehen können, sind mittels des nachgeschalteten Schmiedeprozesses nicht mehr ausheilbar. Die Herausforderung für die hybride Routen Gießen+Schmiedenl besteht daher zum einen in der Abstimmung zwischen Geometrie vor und nach dem Schmiedeschritt und zum anderen der Auslegung geeigneter Parameter für das Gießen und Schmieden, um das die späteren Gebrauchseigenschaften bestimmende Mikrogefüge einzustellen.
Projektpartner
Karlsruher Institut für Technologie,Max-Planck-Institut für Eisenforschung GmbH,Otto Junker GmbH,Rolls-Royce Deutschland Ltd Co KG,Siemens AG
Ansprechpartner/in
Projektinformationen
Laufzeit
1/1/2019 –
12/31/2021
Förderkennzeichen
0324317D
Zuwendungsgeber
Bundesministerium für Wirtschaft und Klimaschutz (BMWK)
Projektträger
Projektträger Jülich
Förderinitiative
Energieforschungsprogramm 6
Geschäftsfeld
Prozessentwicklung und Prototypenfertigung
Projektstatus
in Bearbeitung
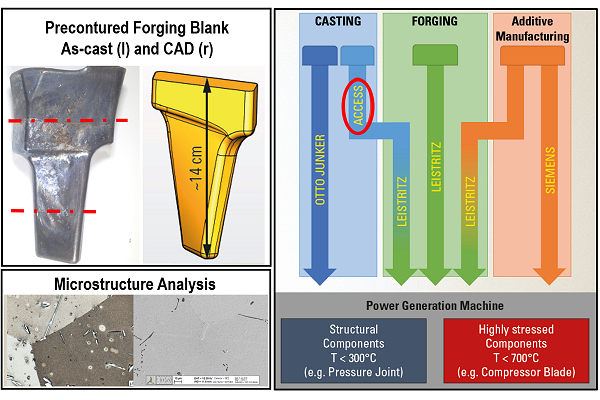